Discovering Aluminum in the Age of Electrification
Aluminum Components Development in the Field
The development of aluminum automotive components is an ongoing effort to create efficient and safe next-generation components encompassing a wide range of factors, such as weight reduction, electrification, automated driving, safety improvement, digitalization, and sustainability. There is a focus on reducing emissions, utilizing renewable energy, and reducing the recyclability and waste of components. UACJ’s automotive component development is based on benchmarking and agile development to flexibly respond to customer requirements.
UACJ Corporation, one of the world’s leading aluminum manufacturers, opened the Mobility Technology Center (MTC) in 2020. It features an integrated system that covers technical planning, materials development, product development, and production technology development. The evaluation and elemental technologies are based on the specialized capabilities of materials and the comprehensive capabilities of materials development, in cooperation with UACJ’s R&D Center.
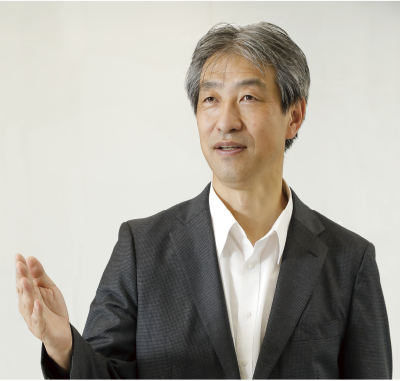
Vice-Director of Mobility Technology Center
Marketing & Technology Division
UACJ Corporation
Akio NIIKURA, Ph.D
Interviewer (MFi): I hear that aluminum components are being used in battery housings for electric vehicles.
Dr. Niikura: Aluminum alloy extruded shapes are widely used in the battery housings of today's mainstream electric vehicles. These aluminum structural members play an important role in terms of safety and battery temperature control. In particular, during a vehicle side impact, the cross-sectional shape of the aluminum extrusions, with a primarily hollow cross-section, absorbs impact energy by deforming under the impact load.
MFi: How do you enhance collision energy absorption performance?
Niikura: In a side impact of a battery housing, it’s difficult to distribute the side impact loads to other structural members, so the side frames of the battery housing must absorb the impact energy. Therefore, it’s important to reduce the weight of the battery housing while meeting the required impact absorption performance. As a method to achieve this, we have established impact energy absorption simulation technology based on UACJ's proprietary know-how, and are developing aluminum structural members.
MFi: How will MTC's components development develop in the future?
Niikura: UACJ has jointly developed bumper beams, crash boxes, and battery housing side frames, which are typical shock-absorbing components for crushable zones, and has accumulated technical information by manufacturing them at domestic and global manufacturing bases. In the future, we would like to promote the modularization of structural members using aluminum alloy extrusion shapes for crushable zones. In parallel, we have also been developing thermal management systems such as cooling channels for battery coolers. We would like to further enhance the manufacturing technology based on UACJ's unique know-how to meet the demand for the development and manufacture of aluminum components for the scalable platforms promoted by automobile manufacturers.
Mainstream lightweight sports car, Mazda MX-5
Development of aluminum alloy bumper
Reinforcement components
The Mazda MX-5 has many components made of aluminum alloy. This bumper was jointly developed by Mazda and UACJ.
The front bumper is the furthest structure from the vehicle's center of gravity. Reducing its weight improves fuel economy and enhances driving performance. Mazda's solution was to use a 7000 series high-strength aluminum alloy. After a comprehensive review, including the manufacturing method, Mazda and UACJ succeeded in fully leveraging the advantages of aluminum by producing a bumper approx. 30% lighter than the previous one.