アルミ合金製コンポーネンツ開発の現場
UACJモビリティテクノロジーセンターの活動。
Advanced Aluminum Technology for the Automobiles of the Future
アルミ自動車部品の開発は、軽量化、電動化、自動運転、安全性向上、デジタル化、持続可能性など多岐にわたる要素を背景に、効率的で安全な次世代のコンポーネンツを目指す取り組みが進行している。車両の燃費向上や電動化への対応は、革新的な技術と持続可能性の観点から急速に進化した。また、排出ガス削減や再生可能エネルギーの活用、部品のリサイクル性や廃棄物削減にも力を入れている。UACJの自動車部品の開発では、ベンチマーキングなどを基にし、アジャイル開発の手法を取り入れ、顧客からの要求変更に柔軟に対応し、効果的なソリューションを提供している。それらの成果は、電動化時代のサプライヤーにとって重要な要件だ。
世界有数のアルミニウム総合メーカーの株式会社UACJは、長年培ってきた自動車部品用アルミ材料の技術とノウハウを結集し、2020年に「モビリティテクノロジーセンター(MTC)」を開設した。MTCは、技術リサーチから技術戦略の立案や事業化の仕組み作りを担う技術企画から、材料開発、先行開発、製品開発、生産技術開発などを一貫体制で行なっている。ベースとなる評価技術や要素技術は、UACJのR&Dセンターとの連携より、アルミ材料の専門力とアルミ部材開発の総合力を駆使している。電動化の流れの中で、アルミ構造部材に求められる要求特性はますます高度化しており、同時に対応のスピードアップも求められている。
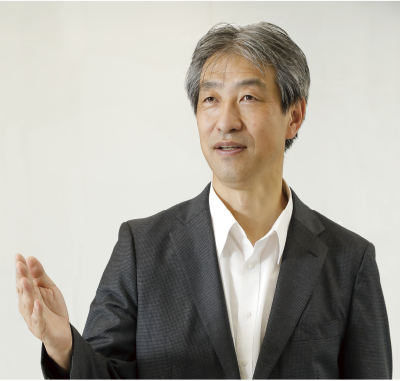
株式会社UACJ
マーケティング・技術本部
モビリティテクノロジーセンター
副センター長 博士(工学)
新倉 昭男
Akio NIIKURA
MFi: バッテリーハウジングにアルミ部材が用いられていると聞きますが。
新倉:現在主流の電気自動車のバッテリーハウジングには、アルミ合金の押出形材が多く利用されています。これらのアルミ構造部材は、安全性の面でもバッテリーの温度管理の面でも重要な役割を果たしています。特に、車両の側面衝突時には、主に中空断面のアルミ押出形材の断面形状が衝突荷重を受けて変形することにより衝撃エネルギーを吸収しますが、この押出形材の断面形状やその構造によって、衝突エネルギー吸収特性が大きく変化します。
MFi: 衝突エネルギー吸収性能というのはどのようにして高めるのでしょうか。
新倉:バッテリーハウジングの側面衝突では、側面に加わる衝突荷重を他の構造部材へ分散することが難しく、バッテリーハウジングのサイドフレームが、それらの衝突エネルギーを吸収する必要が生じます。このため、必要とされる衝撃吸収性能を満たしながら、軽量化を追求することが重要になります。このための手法として、UACJ独自のノウハウによる衝撃エネルギー吸収シミュレーション技術を確立して、アルミ構造部材の開発を行なっています。
MFi: 衝撃エネルギー吸収シミュレーションは、一般的な構造解析でしょうか。
新倉:UACJには、アルミ材料メーカーとして、長年培ってきたアルミ材料の豊富なデータが揃っています。これらをシミュレーションソフトに取り込み、衝撃吸収性能を向上させながら、断面形状や質量を最適化したアルミ押出形材を開発しています。特に、開発した断面形状の押出形材の製造を行なうためには、適合するアルミ材料の強度や延性、成形性、コストなどのバランスでさまざまなノウハウが必要です。製造に最適な材料や軽量化・薄肉化のレビューなども多元的・立体的に行なうことで、線形の構造解析だけでなく非線形性の強い高度な解析を行ない、CAEの精度を向上させています。
MFi: 今後のMTCの部品開発はどのように展開されますか。
新倉:UACJでは、クラッシャブルゾーンの衝撃吸収部材の代表格である、バンパービームやクラッシュボックス、電池筐体サイドフレームなどを共同開発し、国内やグローバルな製造拠点で製造を行なって、技術情報を蓄積してきました。今後は、クラッシャブルゾーンに対応したアルミ合金押出形材による構造部材のモジュール化などを推進したいと思います。また、電池冷却体の冷却流路などのサーマルマネジメントの開発を並行して行なってきました。これらUACJ独自のノウハウによるミュレーション技術をさらに高めて、自動車メーカーの推進するスケーラブルなプラットフォームに対応したアルミ部材の開発・製造のご要望に応えて行きたいと考えています。
ライトウエイトスポーツの本流 Mazda MX-5
アルミ合金製バンパー補強部材の開発
マツダ・ロードスター(MAZDA MX-5)は多くの部品をアルミ合金化したが、そのなかでも注目したいのが、フロントバンパーレインフォースメントだ。このバンパーはマツダとUACJが共同開発した。
厳しくなる衝突安全基準をクリアするために、フロントバンパーに要求される性能は高くなる一方でND型ロードスターでは、最高レベルの安全性能を確保しながら、軽量化もしなくてはならなかった。車体重心からもっとも遠くにあるフロントバンパーの軽量化は、燃費改善だけでなく運動性能のアップにも効いてくる。そこでマツダが採った手段が7000系高強度アルミ合金の採用だ。ロードスター以外のSKYACTIVボディなどで採用しているホットスタンプ材を単純にアルミ合金に材料置換しても、材料強度は鋼材の30 %程度で大幅な軽量化は難しい。そこでマツダとUACJはアルミの優位性を最大限に活かすために、工法を含めてゼロベースで見直しを行ない約30 %軽量化したバンパーを完成させた。
(モーターファンイラストレイテッド vol.206 P13より)